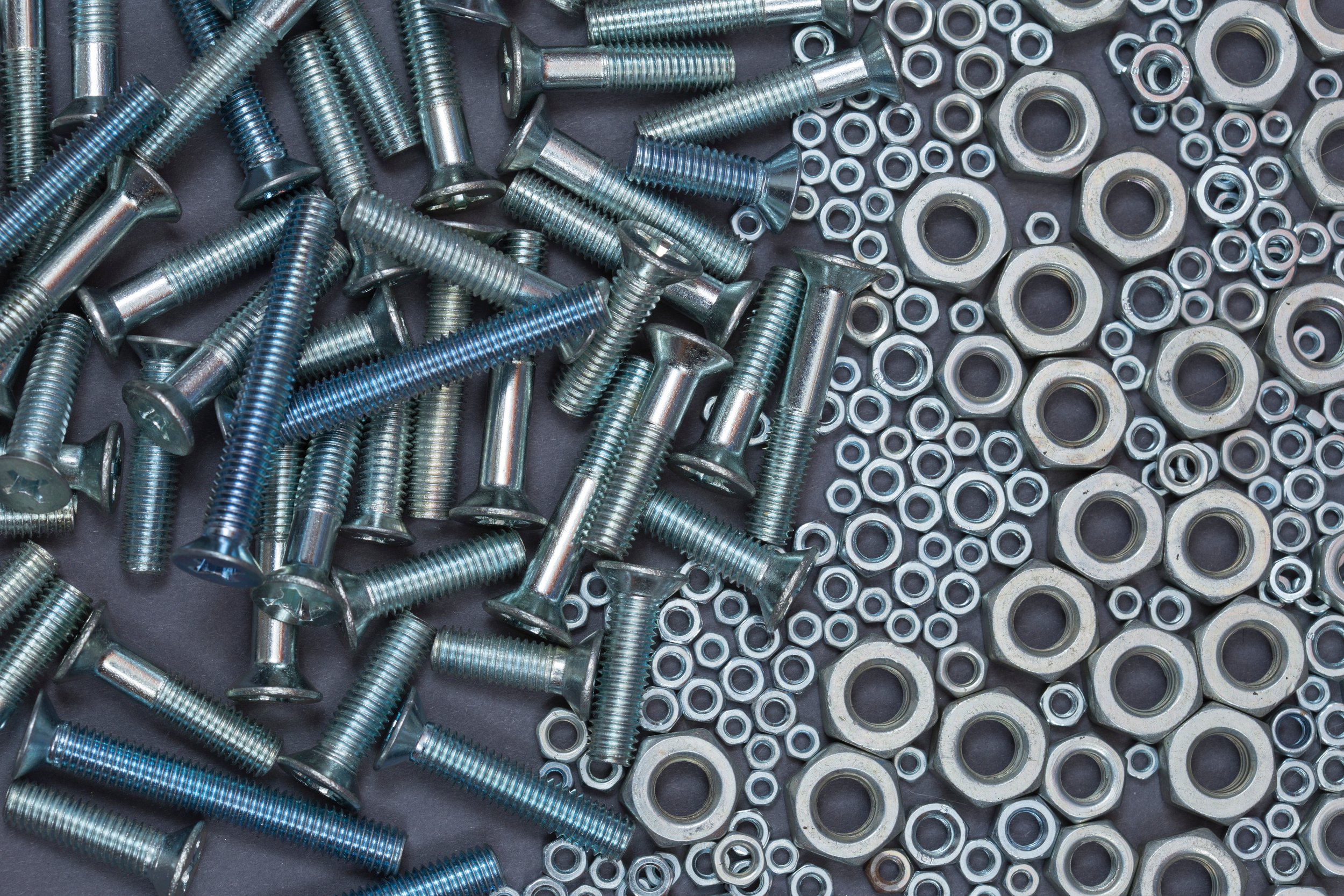
METAL FASTENERS
We strive to provide the parts to you when you want them.
SUPER ALLOY MATERIALS
For Strength, Corrosion Resistance, and High Temperature Applications
The term “superalloy” is applied to alloys which have outstanding high temperature strength, corrosion and oxidation resistance. Many are related to the austenitic stainless steels but are much more highly alloyed, particularly with nickel, chromium and molybdenum in order to enhance their corrosion resistance. These alloys are used to resist extremely corrosive conditions in the energy, power, chemical and petrochemical industries and can maintain strengths at 1000°C, characteristics which exceed that of ordinary steels at room temperature. They are essential in the hottest parts of gas turbines both for power generation and aircraft and are recommended wherever highly corrosive materials are present.
904L
A286
AL6XN
ALLOY 20
ALLOY 50
ALLOY 60
AVESTA® 2205
AVESTA® 254 SMO
CARPENTER® 20/CB3
FERALLIUM® 255
HASTELLOY® X
HASTELLOY® B2
HASTELLOY® B3
HASTELLOY® C22
HASTELLOY® C276
HAYNES® 230
HAYNES® 556
HAYNES® HR-120
HAYNES® HR-160
HAYNES® Ultimet 1233
INCONEL® 600
INCONEL® 601
INCONEL® 625
INCONEL® 718
TANTALUM
WASPALOY®
ZIRCONIUM
Duplex STAINLESS STEEL
The Best Characteristics of Austenitic and Ferritic Stainless Steels in One Alloy.
Duplex stainless steels are called “duplex” because their internal structure consists of 2 different stainless steel types. When duplex stainless steel is melted it solidifies from the liquid phase to a completely Ferritic structure. As the duplex material cools to room temperature, about half of the Ferritic grains transform to Austenitic grains. The result is a alloy that is roughly 50% austenite and 50% ferrite. System 22 carries various duplex stainless products such as, 2205, 2507, 255, LDX 2101, and ZERON® 100.
Strength: Duplex stainless steels are about twice as strong as regular austenitic or ferritic stainless steels.
Toughness and Ductility: Duplex stainless steels have significantly better toughness and ductility than ferritic grades; however, they do not reach the excellent values of austenitic grades.
Corrosion Resistance: Duplex stainless steel grades have a range of corrosion resistance, similar to the range for austenitic stainless steels, i.e from Type 304 or 316 (e.g. LDX 2101©) to 6% molybdenum (e.g. SAF 2507©) stainless steels.
Cost: Duplex stainless steels have lower nickel and molybdenum contents than their austenitic counterparts of similar corrosion resistance. Due to the lower alloying content, duplex stainless steels can be lower in cost. It may also be possible to reduce the thickness of duplex stainless steel, due to its increased yield strength compared to austenitic stainless steel. The combination can lead to significant cost and weight savings compared to a solution in austenitic stainless steels.
TITANIUM ALLOYS
Titanium alloys are metals that contain a Strong. Light. Corrosion and Heat Resistant.
mixture of titanium and other chemical elements. Such alloys have very high tensile strength and toughness. They are light in weight, have extraordinary corrosion resistance and the ability to withstand extreme temperatures.
Titanium Grade 2
Titanium Grade 4
Titanium Grade 5A
Titanium Grade 5B
NICKEL ALLOYS
Look to Nickel and Nickel Alloys For Superior Strength And Corrosion Resistance!
Nickel and Nickel alloys are some of the most corrosion resistant materials on the market today, and are among the toughest structural materials known. Nickel and nickel alloys are non-ferrous metals with high strength and toughness, excellent corrosion resistance, and superior elevated temperature properties.
Gas Turbines
Steam turbine power plants
Medical applications
Nuclear power systems
Chemical and petrochemical industries
Sea/saltwater resistant applications
Common Nickel Alloys: NiCu 400 (Monel) Nicu 405 and NiCuAl 500 (K-Monel)
MARTENSITIC STAINLESS STEEL
The martensitic stainless steel grades are straight chromium steels containing no nickel. They are magnetic and can be hardened by heat treating. The martensitic grades are mainly used where hardness, strength, and wear resistance are required. They are slightly corrosion resistant and can be hardened by heat treating.
Type 410 – The basic martensitic grade. Low cost, general purpose, heat treatable stainless steel. Used widely where corrosion is not severe (air, water, some chemicals, and food acids. Typically used in fastener applications.
Type 416 – Contains added phosphorus and sulfur for improved machinability. Typical applications include screw machine parts.
Type 420 – Contains increased carbon to improve mechanical properties. Typical applications include surgical instruments.
Type 431 – Contains increased chromium for greater corrosion resistance and good mechanical properties. Typical applications include high strength parts such as valves and pumps.
AUSTENITIC STAINLESS STEEL
Austenitic grades are those alloys which are commonly referred to as the “300 series”. The austenitic grades are not magnetic. The austenitic stainless steels, because of their high chromium and nickel content, are the most corrosion resistant of the stainless group providing unusually fine mechanical properties. Austenitic stainless grades cannot be hardened by heat treatment, but can be hardened by cold-working.
Type 304 – The most common grade, it is used in chemical processing, the food and beverage industry, heat exchangers, and milder chemicals.
Type 316 – 316 is used in chemical processing, the paper industry, for food and beverage processing and in more corrosive environments.
Type 317 – Contains a higher percentage of molybdenum than 316 for highly corrosive environments. It is often used in stacks which contain scrubbers.
Type 321 and Type 347 – These grades are often used in the process equipment industry.
COMMON STEEL MATERIALS
We carry many common steel materials for a variety of structural, manufacturing, and industrial applications. We offer all threaded studs, double end studs, socket head cap screws, hex nuts, hex cap screws, socket set screws, heavy hex bolts and other steel fastener configurations. Some of the most common materials we stock are found below.
4140 Steel
4340 Steel
ASTM A193 Grade B16
ASTM A193 Grade B7
ASTM A194 Grade 2H
ASTM A194 Grade 7
ASTM A307 Grade B
ASTM A325
ASTM A490
PRECIPITATION HARDENING STEEL
Precipitation hardening grades offer a combination of fabricability, strength, ease of heat treatment, and corrosion resistance not found in any other class of material. Developed primarily as aerospace materials, many of these steels are gaining commercial acceptance as truly cost-effective materials in many applications.
Grade 17-4PH – A precipitation hardening martensitic stainless steel with Cu and Nb/Cb additions. The grade combines high strength, hardness (up to 572°F / 300°C), and corrosion resistance. Mechanical properties can be optimized with heat treatment, and very high yield strength up to 1100-1300 MPa (160-190 ksi) can be achieved.
Grade 15-5PH – The corrosion resistance of 15-5 Stainless Steel is similar to that of stainless steel type 304. It is most often used for applications in high pressure corrosive environments and for aircraft components.
FERRITIC STAINLESS STEEL
Ferritic stainless steel grades were developed to provide a group of stainless steel materials that resist corrosion and oxidation, while being highly resistant to stress corrosion cracking. These steels are magnetic but cannot be hardened or strengthened by heat treatment. They can, however, be cold worked and softened by annealing. As a group, they are more corrosive resistant than the martensitic grades, but generally inferior to the austenitic grades.
Type 430 – The basic ferritic grade, with a little less corrosion resistance than Type 304. This type combines high resistance to such corrosives as nitric acid, sulfur gases, and many organic and food acids.
Type 405 – Has lower chromium and added aluminum to prevent hardening when cooled from high temperatures. Typical applications include heat exchangers.
Type 409 – Contains the lowest chromium content of all stainless steels and is also the least expensive. Originally designed for muffler stock and also used for exterior parts in non-critical corrosive environments.
Type 434 – Has molybdenum added for improved corrosion resistance. Typical applications include automotive trim and fasteners.
Type 436 –Has columbium added for corrosion and heat resistance. Typical applications include deep-drawn parts.
Type 442 – Has increased chromium to improve scaling resistance. Typical applications include furnace and heater parts.
Type 446 – Contains even more chromium added to further improve corrosion and scaling resistance at high temperatures. Especially good for oxidation resistance in sulfuric atmospheres.
COPPER ALLOYS
Copper alloys are metal alloys that have copper as their principal component. They have high resistance against corrosion. The best known traditional types are bronze, where tin is a significant addition, and brass, using zinc instead. Today the term copper alloy tends to be substituted.
There are as many as 400 different copper and copper-alloy compositions loosely grouped into the categories: copper, high copper alloy, brasses, bronzes, copper nickel, copper–nickel–zinc (nickel silver), leaded copper, and special alloys.
C26000 Cartridge Brass
C95400 Aluminum Bronze
C65500 Silicone Bronze
C36000 Free- Cutting Brass
C46400 Naval Brass
PLASTIC FASTENER MATERIALS
In addition to high quality steel, stainless, titanium and exotic super alloys, System 22, Inc. also offers a wide range of custom plastic materials for use in a wide variety of fastener applications.
Ultem® 2300 – A transparent, amber high performance polymer, Ultem® excels in hot air and water environments. It is hydrolytically stable as well as UV and gamma radiation resistant. It is also inherently flame retardant.
Delrin® – Offering superior durability, exceptional surface rigidity and enhanced dimensional stability, Delrin® also shows minimal water absorption, and has a low coefficient of friction and offers favorable abrasion resistance.
Kynar ® PVDF – A thermoplastic polymer of vinylidene fluoride, it can perform in many applications up to 300°F. It is used extensively in chemical processing applications.
PEEK ® – One of the engineering thermoplastics, it is a rigid plastic with high tensile strength. It offers excellent heat resistance, abrasion resistance, flame resistance and hydrolysis resistance. PEEK® is commonly used in various fields like outdoor action equipment, automobiles, semiconductor equipment, and the modular cleanroom to produce medical implants.
Nylon – All grades maintain great strength and offer extremely good wear resistance. In addition it can withstand sustained contact with a wide variety of chemicals, alkalis, diluted acids etc. Economically Nylon is an excellent product, and approximately ½ the weight of aluminum. This material is also available in glass-filled, further extending it’s mechanical properties.
PVC (Poly Vinyl Chloride) – PVC offers outstanding corrosion and weather impedance. This material is also self-extinguishing per UL flammability tests and has a high strength to weight ratio.